Mechanical Systems
The frame consists on a single chassis, formed by several square hollow bars which endows the submarine with high hardness and strength, without compromising it´s weight.. We have used aluminium 6063 with T5 heat treatment that allows us to weld it using TIG. The aluminium 6063 offer us excellent quality in marine environment and high mechanical resistance. Another benefit of this material is the magnetic shield that protects our systems. The choice for this material was mostly due to the thermal conduction and the magnetic shield. The whole electronic systems will be placed inside plastic square boxes that are fully isolated and protected against moisture.
FRAME

MANOEUVRE SYSTEM
The manoeuvre system is a consequence of the type of propulsion and our desire of having a submarine with maximum possible mobility. Last year, our AUV used 22 valves to control the flow that came from the pumps through pipes. This year we have designed a multivalve that allows us to improve the flow with a lighter solution.


The 4 multivalves are placed in extreme positions of the vehicle in order to generate enough torque to turn in all three dimensions. This valve system allows us to manoeuvre at 4 or 5 different speeds. These speeds enable our vehicle to achieve very precise positions. This total control of the course is possible because of the continuous operational regime of the pumps. This regime also reduces vibrations and noise that affect the data acquired systems, and the energy consumption due to the lack of turn on/off during the mission. Finally, after testing commercial valve systems, we manufactured special butterfly valves which are actuated by waterproof servos.
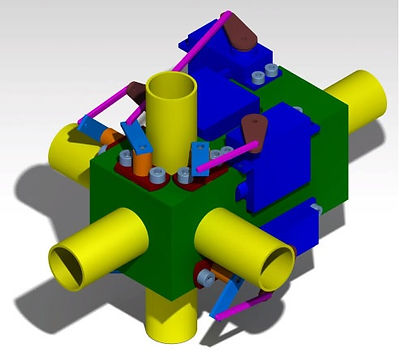
EXTERNAL ENCLOSURES
The robot has a central watertight lightweight strong HPX resin enclosure (462 x 307 x 132 [mm], 3,27 [kg]) with most of the electronics. It also has 4 smaller drybox enclosures (174 x 115 x 91 [mm], 0,18 [kg]) near the multivalves with STM32F3DISCOVERY boards for servomotors controlling, inertial information for sensor fusion, and temperature status.
Each camera has its own aluminum watertight enclosure and is connected to the central enclosure by USB.

HULL
The new hull design offers excellent agility and stability. Extensive testing with Next Limit’s xflow software helped us improving the hull for a better behavior on ocean conditions. The first step was build a model from the hull in extruded polystyrene foam, coating with carbon fiber, and finally another coat of epoxy resin. The carbon fiber properties are high stiffness, high tensile strength, low weight, high chemical resistance, high temperature tolerance and low thermal expansion.
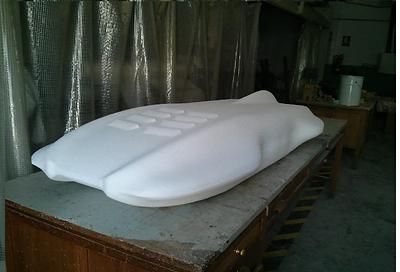
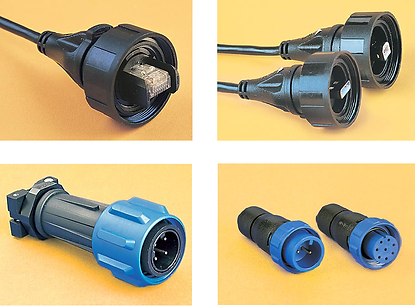
WATERTIGHTS CONNECTORS
In order to guarantee the waterproof of the boxes and other systems, we have used low cost watertight commercial connectors that are customized to exceed the manufacturer specifications, so we can achieve 30 meters depth.
ACTUATORS
PERAL2013 actuators system is comprised of 4 pumps, 3 grabbers, 2 droppers and torpedo launchers, ventral cameras and servomotors.
Pumps
Droppers
Our AUV uses four centrifugal pumps in permanent operation which are distributed vertically in order to help controlling the global buoyancy. The choice of this type of pumps is due to the necessity of having high water flow with high speed and low pressure. High pressure flow would mean larger pumps and more pressure drop; consequently, we would need more energy, more batteries, stronger structure, etc.
Hence the choice of these centrifugal pumps, it is important to note that the pumps are integrated into the hull. This implies that the hull is partially flooded. This improves the buoyancy and stability of our robot. In order to not increase the wetted surface, however, we decided to cover our submarine and put the pumps inside of it.
This way, the own pumps absorb part of the friction and generate a false shield which makes the inertia lower.
Ventral cameras
Grabbers
PERAL2013 uses 3 grabbers in order to achieve the task of recovery object on the course. The grabbers consist of aluminum claws with brass sleeves in their joints. They can open for about 50 [mm] and employ a servo motor. They can pick up objects of up to 10 [kg] with ease. They are placed on the ventral part of the submarine.

The droppers consist on two pipes each one with an aluminum sphere and a servomotor that releases the marker at the desired moment.
Servomotors
Torpedo Launcher
A servomotor allows the ventral cameras to turn 45º so they can help controlling the approach of the vehicle to the recovery object, and help the claws to make a more efficiently grab the item.

The PERAL2013 carries two smart torpedoes, each one on an aluminum pipe, with a servomotor controller that releases the torpedo on ignition. They include an optical link with high noise immunity between the CCS (Central Control System) and the torpedoes in order to set them and check their status.
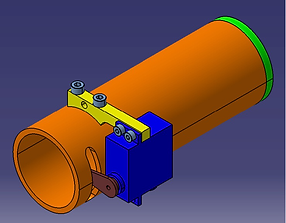
The robot uses 28 watertight servomotors to actuate with the following systems, (2) the torpedo launchers, (20) multivalve, (1) ventral cameras, (3) grabbers and (2) droppers. It consists of a 3 pole motor coupled to a sensor for position feedback. The torque is 11.6 [kg/cm].
